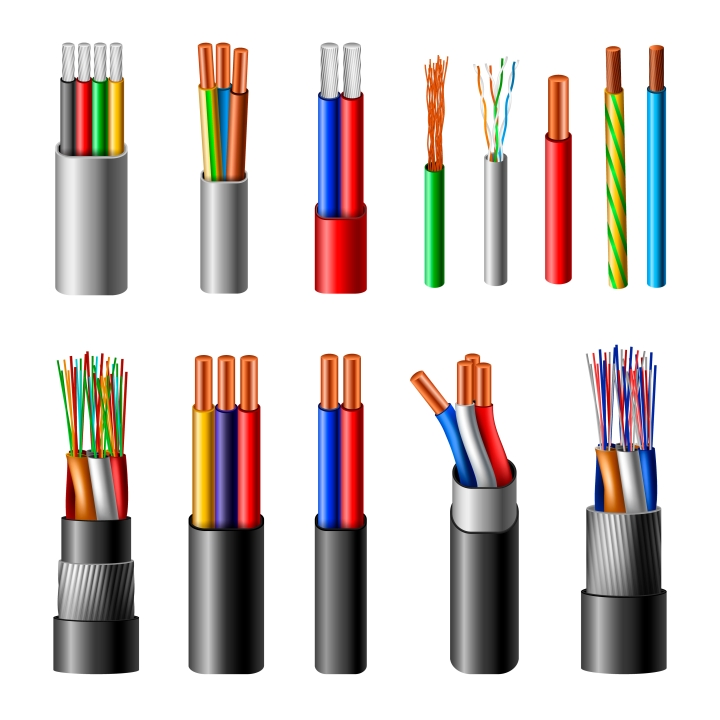
Cables play a vital role in the functioning of modern industries. Here are some of the key reasons why cables are important in industries:

- Power transmission: Cables are used to transmit electrical power from one point to another. They are used to connect power sources such as generators and transformers to distribution networks, and to distribute power within industrial facilities. Without cables, it would not be possible to transmit power over long distances or to power industrial machinery.
- Data transmission: In addition to power transmission, cables are also used to transmit data in industrial settings. Communication cables are used to transmit signals from sensors, controllers, and other devices that are used to monitor and control industrial processes. These cables are critical for ensuring that industrial processes are monitored and controlled effectively.
- Safety: Cables play an important role in ensuring the safety of industrial workers and equipment. They are used to power equipment, such as motors and pumps, and to provide lighting for work areas. Cables must be designed and installed to meet strict safety standards to prevent electrical hazards and to ensure the safe operation of industrial equipment.
- Durability: Industrial cables must be able to withstand harsh environmental conditions, including exposure to heat, cold, moisture, and chemicals. They must also be able to withstand physical stress, such as abrasion and bending. Industrial cables are designed to be durable and to provide reliable service over long periods of time.
- Cost effectiveness: Cables are a cost-effective solution for transmitting power and data in industrial settings. They are often more cost-effective than other solutions, such as wireless transmission, and they require less maintenance and replacement over time.
In summary, cables are an essential component of modern industrial systems. They are used to transmit power and data, ensure safety, withstand harsh environments, and provide a cost-effective solution for powering industrial equipment.
Informative Details
Cable is a common term used to describe a bundle of wires or cords that are used to transmit electrical power or signals. There are many different types of cables, each designed for specific purposes and applications.

The most common type of cable is the power cable, which is used to deliver electrical power from a source, such as a power plant or generator, to a destination, such as a home, office, or industrial facility. Power cables are typically made of copper or aluminum wires coated with insulation to protect against electrical shock and other hazards. They may also have additional layers of protective materials, such as shielding or armor, to guard against environmental factors like moisture, heat, and physical damage.
Another type of cable is the data cable, which is used to transmit digital signals between devices, such as computers, phones, and other electronic equipment. Data cables come in many varieties, including USB cables, Ethernet cables, and HDMI cables, each with specific features and capabilities to suit different needs. For example, USB cables are used to transfer data and charge devices, Ethernet cables are used to connect computers and other devices to a local area network (LAN), and HDMI cables are used to transmit high-definition video and audio signals.
Other types of cables include fiber optic cables, which use light to transmit information over long distances, and coaxial cables, which are commonly used for cable TV and internet connections. There are also specialized cables for specific applications, such as automotive cables for cars, aircraft cables for airplanes, and marine cables for boats and ships.
Cable technology is constantly evolving, with new materials, designs, and features being developed to meet the ever-increasing demands of modern society. As a result, cables have become an essential part of our daily lives, enabling us to power our homes and businesses, communicate with each other, and access the vast array of digital content available today.
Selection for Industries and it’s sizing selection
Electrical cable selection for industries involves choosing the appropriate type of cable and determining the right size to meet the specific electrical requirements of the application. There are several factors that should be taken into account when selecting the appropriate cable for industrial applications, including the environment in which the cable will be used, the amount of current that will be carried, and the distance over which the cable will be run.

The following are the steps involved in selecting the right cable and sizing it for an industrial application:
- Determine the type of cable required: There are many types of cables available, each with specific features and properties. Some of the most common types of industrial cables include power cables, control cables, instrumentation cables, and communication cables. The type of cable needed will depend on the application and the specific requirements of the system.
- Determine the operating voltage and current: The operating voltage and current are critical factors to consider when selecting the right cable. The voltage and current rating of the cable should match the requirements of the application to ensure safe and reliable operation.
- Determine the distance of the cable run: The length of the cable run is a crucial factor in determining the appropriate cable size. Longer cable runs require larger cables to compensate for the voltage drop that occurs over distance.
- Calculate the voltage drop: The voltage drop is the reduction in voltage that occurs over the length of the cable run. This can cause a loss of power and affect the performance of the system. It is important to calculate the voltage drop and choose a cable with the appropriate size to minimize it.
- Select the appropriate cable size: Once the voltage drop has been calculated, the appropriate cable size can be selected. The cable size should be large enough to minimize the voltage drop and ensure safe and reliable operation of the system.
In summary, electrical cable selection for industrial applications involves choosing the right type of cable and determining the appropriate size based on the operating voltage and current, the length of the cable run, and the voltage drop. By following these steps, it is possible to select the appropriate cable that meets the requirements of the system and ensures safe and reliable operation.
Determine the types and requirment
To determine the type of cable required for a specific application, it is important to consider the following factors:
- Electrical requirements: The first consideration is the electrical requirements of the system, including the voltage, current, and frequency of the electrical power supply. These requirements will determine the appropriate type of cable to use, such as power cables, control cables, instrumentation cables, or communication cables.
- Environmental conditions: The second consideration is the environment in which the cable will be used. Industrial environments can be harsh, with exposure to chemicals, moisture, and extreme temperatures. The cable selected should be able to withstand these conditions and operate safely and reliably.
- Mechanical requirements: The third consideration is the mechanical requirements of the application. The cable selected should be able to handle the mechanical stresses placed upon it, such as bending, twisting, or pulling.
- Code requirements: The fourth consideration is any applicable code requirements, such as the National Electrical Code (NEC). These codes specify minimum requirements for cable types based on the application, so it is important to review the codes and select a cable that meets the minimum requirements.
- Cost: The final consideration is the cost of the cable. There may be many different cable types that could be used for a specific application, and cost can be a significant factor in selecting the appropriate cable.
Once all of these factors have been considered, it is possible to determine the type of cable required for the specific application. By choosing the appropriate cable type, it is possible to ensure safe and reliable operation of the system and minimize the risk of electrical hazards or equipment failure.
Types of Cables
There are many different types of cables, each with their own unique features and intended uses. Here are some of the most common types:

- Coaxial Cable: Coaxial cable is a type of cable consisting of an inner conductor, insulating layer, metallic shield, and outer cover. It is often used for video and data transmission applications, including cable TV, internet, and security systems.
- Twisted Pair Cable: Twisted pair cable is made up of two copper wires twisted together. It is commonly used for telecommunications and computer networking applications.
- Fiber Optic Cable: Fiber optic cable is made of glass or plastic fibers that transmit light signals over long distances. It is used for high-speed data transmission and telecommunications applications.
- Shielded Cable: Shielded cable is a type of cable that has a metallic shield to protect against electromagnetic interference. It is commonly used in industrial and automotive applications.
- Flat Ribbon Cable: Flat ribbon cable is a type of cable that consists of multiple parallel conductors that are laid flat and encased in a single sheath. It is commonly used for internal computer and electronics connections.
- Multicore Cable: Multicore cable is a cable that consists of multiple insulated conductors within a single sheath. It is commonly used in industrial and automotive applications.
- Armoured Cable: Armoured cable is a cable that has an additional layer of protection, typically a metal sheath or braid, to protect against physical damage. It is commonly used in outdoor and underground installations.
- High-Temperature Cable: High-temperature cable is a cable that is designed to withstand high temperatures, typically up to 200°C or more. It is commonly used in industrial and automotive applications where high temperatures are present.
These are just a few of the many types of cables available. The choice of cable type will depend on the intended application, the operating environment, and other factors such as electrical requirements, mechanical strength, and cost.
Determine the operating voltage and current
To determine the operating voltage and current for an electrical system, it is important to follow these steps:

- Consult the equipment specifications: The first step is to consult the equipment specifications to determine the operating voltage and current required by the equipment. This information should be readily available in the documentation provided by the equipment manufacturer.
- Measure the voltage and current: If the equipment specifications are not available, or if the system is not yet installed, it may be necessary to measure the voltage and current using a multimeter. The multimeter can be used to measure the voltage and current of the electrical circuit to determine the operating values.
- Consider the load requirements: It is important to consider the load requirements of the equipment being used to determine the operating voltage and current. The load requirements will determine the amount of power that needs to be delivered to the equipment, and the operating voltage and current will depend on the power requirements of the load.
- Consider the electrical distribution system: The operating voltage and current will also depend on the electrical distribution system being used. The voltage and current available in the system will determine the appropriate equipment and cables needed to deliver power to the load.
- Consider safety factors: It is important to consider safety factors when determining the operating voltage and current. Electrical systems should be designed with a safety factor in mind to ensure safe and reliable operation. This will help to prevent overloading of the system and reduce the risk of electrical hazards.
By following these steps, it is possible to determine the operating voltage and current required for an electrical system. Once the operating values are known, it is possible to select the appropriate equipment and cables needed to deliver power to the load safely and reliably.
Calculate the voltage drop
To calculate the voltage drop in an electrical cable, the following steps should be followed:

- Determine the length of the cable: The first step is to determine the length of the cable run. The length of the cable will have a direct impact on the amount of voltage drop that occurs.
- Determine the resistance of the cable: The resistance of the cable is another important factor in calculating the voltage drop. The resistance of the cable will depend on the size of the cable, the material it is made of, and its temperature rating.
- Determine the current in the circuit: The current in the circuit is the amount of electrical current that is flowing through the cable. This value should be measured or obtained from the equipment specifications.
- Calculate the voltage drop: The voltage drop can be calculated using Ohm’s law, which states that voltage equals current multiplied by resistance. The formula for calculating voltage drop is: Voltage drop = Current x Resistance x Length Where:
- Voltage drop is in volts (V)
- Current is in amperes (A)
- Resistance is in ohms (Ω)
- Length is in meters (m)
The calculated voltage drop should be compared to the allowable voltage drop for the application. Allowable voltage drops are typically specified in the equipment or system specifications and should be used to ensure that the cable selected will not cause the system to operate outside its desired range.
By following these steps, it is possible to calculate the voltage drop in an electrical cable and select the appropriate cable size to minimize the voltage drop and ensure safe and reliable operation of the system.
Select the appropriate size
Selecting the appropriate cable size is a crucial step in ensuring safe and reliable operation of an electrical system. The following steps should be followed to select the appropriate cable size:

- Determine the current-carrying capacity of the cable: The current-carrying capacity of the cable is the maximum amount of current that the cable can safely carry without overheating. This value can be found in the cable manufacturer’s datasheet or in cable sizing tables provided by industry standards.
- Determine the maximum current that the circuit will carry: The maximum current that the circuit will carry can be obtained from the equipment specifications or by measuring the actual current with a clamp meter.
- Calculate the minimum cable size: Once the maximum current that the circuit will carry is known, the minimum cable size required can be calculated. This can be done by dividing the maximum current by the current-carrying capacity of the cable and selecting the next largest standard cable size that meets or exceeds the calculated minimum size.
- Consider other factors: In addition to current-carrying capacity, other factors should also be considered when selecting the appropriate cable size. These factors include voltage drop, ambient temperature, and the installation environment. It is important to ensure that the selected cable can handle the expected voltage drop and that it is rated for the maximum temperature that it will be exposed to in the installation environment.
- Consult industry standards: It is also important to consult industry standards and regulations for guidance on selecting the appropriate cable size. For example, the National Electrical Code (NEC) in the United States provides guidelines for selecting the appropriate cable size based on the type of installation and the maximum current that the circuit will carry.
By following these steps and considering all relevant factors, it is possible to select the appropriate cable size for a given application, ensuring that the system operates safely and reliably.
Segregation of cables base of Voltage Level
In industrial settings, cables are often segregated based on their voltage levels to ensure safety and to comply with relevant regulations. Here is a general guideline for segregating cables based on voltage levels:

- Low voltage (LV) cables: LV cables are typically used for transmitting electrical power at voltages up to 1 kV. These cables are commonly used in buildings and small-scale industrial settings. They are often installed in conduits or trays, and they may be separated from higher voltage cable by physical barriers or by distance.
- Medium voltage (MV) cable: MV cable are used for transmitting electrical power at voltages between 1 kV and 33 kV. These cable are commonly used in larger industrial facilities and in power distribution networks. They are often installed in underground ducts or on overhead lines, and they may be separated from lower and higher voltage cable by physical barriers or by distance.
- High voltage (HV) cable: HV cable are used for transmitting electrical power at voltages above 33 kV. These cable are typically used in large-scale power transmission and distribution networks. They are often installed in underground ducts or on overhead lines, and they may be separated from lower voltage cable by physical barriers or by distance.
In addition to voltage level, cables may also be segregated based on other factors, such as their function, type, and insulation. Segregating cables based on these factors can help to ensure safety and to prevent interference between different types of cables. It is important to follow relevant regulations and guidelines when designing and installing cable systems in industrial settings to ensure that they are safe and reliable.
Color Codes for Cables
In industries, cable are often identified and labeled using color codes for easy identification and maintenance. The specific color codes used may vary depending on the industry, location, and standards adopted, but some commonly used color codes for cable in industries are:

- Power cables:
- Black: Used for line or phase conductors.
- Red: Used for phase B conductor.
- Blue: Used for phase C conductor.
- White or gray: Used for neutral conductor.
- Green or green/yellow striped: Used for protective earth or ground conductor.
- Control cables:
- Black: Used for power or common connections.
- Red: Used for emergency stop or emergency power off.
- Yellow: Used for stop or off signals.
- Green: Used for start or on signals.
- Blue: Used for forward motion or positive signals.
- White: Used for reverse motion or negative signals.
- Communication cables:
- Orange: Used for fiber optic cables.
- Blue: Used for data transmission cables.
- White: Used for audio cables.
- Yellow: Used for video cables.
It is important to note that the color codes used for cable in industries may differ between countries and regions, and may also be subject to specific standards and regulations. It is therefore essential to consult the relevant standards and regulations in your area to ensure that the correct color codes are used for cable identification and labeling.
Short-circuit Capacity Industrial Cables
Short-circuit capacity refers to the ability of a cable to withstand the thermal and mechanical stresses that occur during a short-circuit fault. In industrial settings, short-circuit capacity is an important consideration when selecting cables, as short-circuit faults can cause significant damage to equipment, systems, and personnel.
The short-circuit capacity of a cable is influenced by several factors, including:
- Conductor size: The size of the cable’s conductors affects its short-circuit capacity. Larger conductors have a higher short-circuit capacity and can carry more current without being damaged.
- Insulation material: The type of insulation material used in the cable also affects its short-circuit capacity. Insulation materials with higher thermal resistance have a higher short-circuit capacity and can withstand more heat during a fault.
- Cable design: The design of the cable, including the number of conductors, the type of insulation, and the overall construction, can also affect its short-circuit capacity.
To ensure that industrial cables have adequate short-circuit capacity, they are often tested to industry standards, such as the International Electrotechnical Commission (IEC) 60287 standard, which provides guidelines for calculating the short-circuit capacity of cables.
In addition to selecting cables with sufficient short-circuit capacity, it is also important to ensure that the entire electrical system, including protective devices such as fuses and circuit breakers, is designed and installed to protect against short-circuit faults. Proper system design and protection can help prevent damage to equipment, systems, and personnel and ensure safe and reliable operation of the electrical system.
Specification of Electrical Industrial Cables
Electrical industrial cables are specified using a range of parameters that define their electrical, mechanical, and environmental properties. Here are some of the key specifications for electrical industrial cables:

- Voltage rating: The voltage rating is the maximum voltage that the cable can safely carry. This is an important specification to consider when selecting cables for high voltage applications.
- Current rating: The current rating is the maximum current that the cable can safely carry. This specification is important for selecting cables that can handle the expected current load.
- Conductor material: The conductor material is the material used for the cable’s conductive core. Common materials include copper, aluminum, and their alloys.
- Insulation material: The insulation material is the material used to insulate the conductive core of the cable. Common materials include PVC, XLPE, rubber, and Teflon.
- Shielding: Shielding is a protective layer that is added to some cables to protect against electromagnetic interference (EMI) or radio frequency interference (RFI).
- Temperature rating: The temperature rating is the range of temperatures at which the cable can operate safely. This specification is important for selecting cables that can operate in extreme temperature conditions.
- Jacket material: The jacket material is the outer protective layer of the cable. Common materials include PVC, rubber, and thermoplastic elastomers.
- Flexibility: The flexibility of the cable refers to its ability to bend and flex without damage. This specification is important for selecting cables that will be used in applications that require frequent movement.
- Flame resistance: Flame resistance is the ability of the cable to resist burning or spreading flames in the event of a fire.
- Abrasion resistance: Abrasion resistance is the ability of the cable to resist damage from rubbing or scraping against other surfaces.
By considering these and other specifications, it is possible to select the appropriate industrial cable for a particular application, ensuring safe and reliable operation in even the most demanding industrial environments.
Indian Make of Cables
There are many cable manufacturers in India that produce a wide range of cables for various applications. Here are some well-known Indian manufacturers of cables:
- Polycab India Limited: Polycab is a leading Indian cable and wire manufacturer, offering a range of products including power cable, control cable, communication cable, and flexible cable.
- Havells India Limited: Havells is a well-known Indian electrical products manufacturer that produces a range of cable and wires, including power cable, control cable, and communication cable.
- Finolex Cables Limited: Finolex is one of the largest manufacturers of electrical and telecommunication cables in India. They offer a wide range of products including power cables, control cables, and communication cables.
- KEI Industries Limited: KEI Industries is a leading Indian cable manufacturer, offering a range of products including power cables, control cables, and specialty cables for industrial and infrastructure applications.
- V-Guard Industries Limited: V-Guard is a well-known Indian manufacturer of electrical products, including cables and wires for power distribution and communication.
- Universal Cables Limited: Universal Cables is a leading Indian cable manufacturer, producing a range of products including power cables, control cables, and communication cables for various applications.
These are just a few examples of Indian cable manufacturers. There are many other Indian manufacturers that produce high-quality cables for different applications, both for the domestic and international markets.

Cables & Wires
