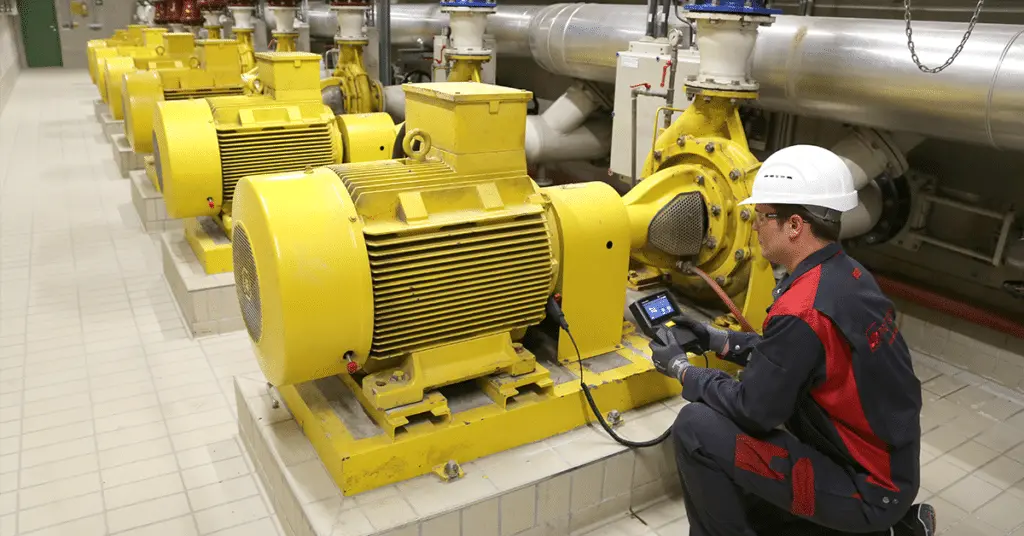
In the expansive landscape of Industrial Manufacturing, the pursuit of optimal efficiency stands as a linchpin for success. Amidst the tools and strategies that have reshaped industries, one standout concept takes the spotlight – Condition Monitoring. This article embarks on a detailed exploration of this transformative idea, unraveling its profound significance and its role in elevating industrial processes.
“In the world of manufacturing, foreseeing issues is as crucial as fixing them – that’s the power of predictive analytics.”
Unraveling the Essence of Condition Monitoring
In the intricate web of machinery and operations, Condition Monitoring emerges as a beacon of proactive management. Rather than relying on reactive responses to malfunctions, it introduces a paradigm shift — envision it as a routine health check-up for machines, a preventative approach aimed at sidestepping breakdowns and mitigating the financial strain of unexpected repairs.
The Fundamental Pillars of Condition Monitoring
At its nucleus, Condition Monitoring revolves around the continuous surveillance and analysis of machine data. This encompasses a spectrum of parameters, including vibrations, temperature, pressure, and other critical indicators. Through the meticulous tracking of these factors, businesses gain the ability to discern irregularities that may forewarn of potential issues.
The Mechanics of Condition Monitoring
Let’s peel back the layers to comprehend the inner workings of Condition Monitoring:
1. Data Collection: Eyes and Ears of Machines
Sensors, akin to the eyes and ears of a system, are strategically deployed to harvest information from machines. These sensors operate in real-time, acting as vigilant custodians of the machine’s well-being.
2. Data Analysis: Deciphering the Machine’s Language
The collected data undergoes a sophisticated analysis, powered by advanced algorithms. This analytical process serves as the interpreter, detecting deviations from the norm that might signal an impending problem.
3. Early Detection: Nipping Issues in the Bud
Armed with the insights from data analysis, businesses can take proactive measures. Whether it’s scheduling maintenance or replacing a specific component, this early intervention prevents the escalation of potential issues.
Unleashing the Potential: Condition Monitoring and Industrial Efficiency
Condition Monitoring transcends the realm of averting breakdowns; its impact resonates profoundly in the realm of efficiency enhancement.
1. Downtime Reduction: Uninterrupted Operations
By addressing issues in their infancy, businesses can substantially slash downtime. This translates to more operational hours, steering clear of emergency repairs and fostering a smoother workflow.
2. Cost Savings: The Economics of Prevention
Preventive maintenance, facilitated by Condition Monitoring, proves to be a more economically viable option than reactive measures. The avoidance of costly repairs and replacements contributes significantly to long-term fiscal savings.
3. Enhanced Productivity: A Ripple Effect
Smoothly operating machines breed enhanced productivity. With uninterrupted processes, the output naturally witnesses a boost, playing a pivotal role in the overarching success of industrial operations.
Navigating Challenges in the Realm of Condition Monitoring
While the benefits of Condition Monitoring are undeniable, navigating its implementation poses certain challenges.
1. Initial Investment: A Strategic Commitment
Implementing a robust Condition Monitoring system demands an initial investment. However, viewing it as a strategic commitment reveals the long-term dividends it pays in the form of efficiency and cost savings.
2. Data Management: Taming the Information Deluge
The copious amounts of data generated by Condition Monitoring can be overwhelming. Investing in advanced data management systems becomes imperative to harness the full potential of this technology.
Peering into the Future: Trends in Condition Monitoring
As technology evolves, so does Condition Monitoring. Here are some emerging trends poised to shape its trajectory:
1. Predictive Analytics: Anticipating Challenges
Moving beyond prevention, predictive analytics aspires to forecast issues before they manifest in the data, ushering in a new era of foresight.
2. Integration with IoT: The Synergy Unleashed
The integration of Condition Monitoring with the Internet of Things (IoT) marks a seamless union, promising more comprehensive and interconnected monitoring capabilities.
Practical Application:
Let’s imagine a factory that produces widgets. With Condition Monitoring, sensors are placed on the machines. These sensors continuously check the vibrations and temperatures. One day, the data shows a slight deviation. Instead of waiting for a breakdown, the maintenance team is alerted. They find a small issue with a crucial part and fix it before it causes a major problem. This prevents the machines from stopping suddenly, ensuring a smooth production flow. The company avoids costly repairs and keeps the production line running efficiently.
Real-world Impact:
In a real-world scenario, a car manufacturing plant embraces Condition Monitoring. One of the assembly line robots starts showing unusual vibrations. With early detection, the maintenance team identifies a worn-out component. They replace it before it fails, preventing a halt in production. This quick action not only saves the company money on emergency repairs but also ensures that cars are manufactured without delays, meeting customer demand.
“Condition Monitoring ensures machines speak before they shout, saving time and money.”
In Summation
In the tapestry of Industrial Manufacturing, Condition Monitoring stands as a cornerstone. Its capacity to predict and preempt issues not only saves businesses financial resources but also paves the way for a more streamlined and efficient operation. Embracing this technology transcends being a mere choice; it emerges as a necessity for those striving to maintain a competitive edge in the dynamic landscape of industrial manufacturing. As we peer into the future, the continued evolution of Condition Monitoring promises not just efficiency but a profound transformation of industrial landscapes.

Allen‑Bradley PLC Systems

Delta PLC Systems

Automation
