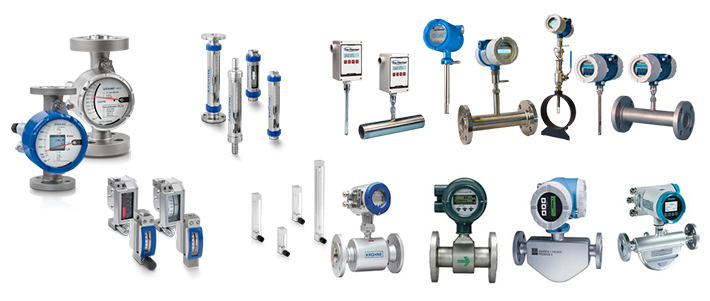
“In the world of manufacturing, calibration is the silent hero, ensuring precision and reliability in every operation.”
In the world of making things, where machines hum and gears turn, one crucial term keeps everything ticking just right: Calibration. Let’s take a stroll through this simple yet powerful concept, exploring how it guarantees accuracy and reliability in the vast landscape of industrial manufacturing.
What is Calibration?
Calibration is like a friendly check-up for machines. Imagine you have a ruler, and you want to be sure it measures inches correctly. Calibration is the process that makes sure your ruler is spot-on, so when you measure, you know it’s right.
Instruments and Machines Need Love Too
Machines in factories, just like your ruler, use instruments to measure things. These instruments need to be calibrated regularly. It’s like giving them a tune-up, making sure they’re not telling fibs when they measure stuff.
Why is Calibration Important?
Accuracy Matters
In the world of industrial manufacturing, precision is the name of the game. Imagine building a car where all the parts need to fit together perfectly. Calibration ensures the machines make accurate measurements, so each part fits like a glove.
Reliability Keeps the Wheels Turning
Reliability is like having a trustworthy friend. In manufacturing, machines need to be reliable. Calibrating them ensures they stay consistent, like a loyal companion who never lets you down.
How Does Calibration Work?
A Simple Process
Calibration is not rocket science; it’s more like a well-organized dance. First, you have a standard—a known measurement that’s absolutely right. Then, you compare this standard with what your machine is telling you. If they match, great! If not, it’s time to adjust until they sync up perfectly.
Regular Check-ups
Like going to the doctor for a regular health check, machines need routine calibration. It’s a preventive measure to catch any issues early on, ensuring the machines keep doing their job without any hiccups.
Common Calibration Methods in Industrial Manufacturing
1. Visual Calibration
This is the “seeing is believing” method. Engineers use their eyes to ensure that machines are producing the right results. It’s like checking that your clock shows the correct time by looking at it.
2. Mechanical Calibration
Think of this as giving your machine a workout. Engineers physically adjust the components to make sure everything is in perfect harmony. It’s like tightening a loose screw to keep things running smoothly.
3. Electronic Calibration
In the digital age, machines often rely on electronic signals. Engineers use electronic calibration to make sure these signals are telling the truth. It’s like double-checking your phone battery percentage to make sure it’s accurate.
Benefits of Calibration in Industrial Manufacturing
1. Cost Savings
Calibration prevents mistakes, reducing the likelihood of producing faulty products. This means fewer errors, less waste, and more money saved in the long run.
2. Quality Assurance
Calibration ensures that each product meets the required standards. It’s like having a quality control superhero, making sure everything leaving the factory is top-notch.
3. Regulatory Compliance
In some industries, there are rules and regulations to follow. Calibration helps companies stay on the right side of the law, ensuring their processes meet the necessary standards.
Challenges in Calibration
1. Downtime Woes
Calibrating machines may mean a temporary pause in production. It’s like taking a breath to stretch before a big race – a short pause for long-term benefits.
2. Skill Requirements
Calibration is a skilled job. Engineers need to know the ins and outs of the machines they’re working on. It’s like having a car mechanic who knows every nook and cranny of your vehicle.
3. Practical Application
Let’s say you have a company making widgets. Calibration ensures the machines measuring widget sizes are spot-on. If calibration isn’t done, your widgets might end up too big or too small, causing customer complaints. Regular calibration ensures your widgets are just right, keeping customers happy and your business thriving.
4. Real-world Impact
Imagine a car manufacturer forgetting to calibrate their robots welding car parts. Without proper calibration, the welds might be weak, leading to cars that aren’t safe. Calibration here ensures every car on the road is sturdy and secure, impacting not just the manufacturer’s reputation but the safety of countless drivers.
“Calibration ensures our machines speak the truth, giving us confidence in every product we make.”
Conclusion
So, there you have it – calibration in industrial manufacturing. It’s the unsung hero that ensures everything runs like clockwork. Just like calibrating your favorite recipe to get the perfect taste, in manufacturing, it’s about getting the perfect product every time. So, the next time you see a well-made car or a precisely crafted gadget, remember, calibration played its part behind the scenes, ensuring accuracy and reliability in the world of industrial manufacturing.

Temperature Transmitter
