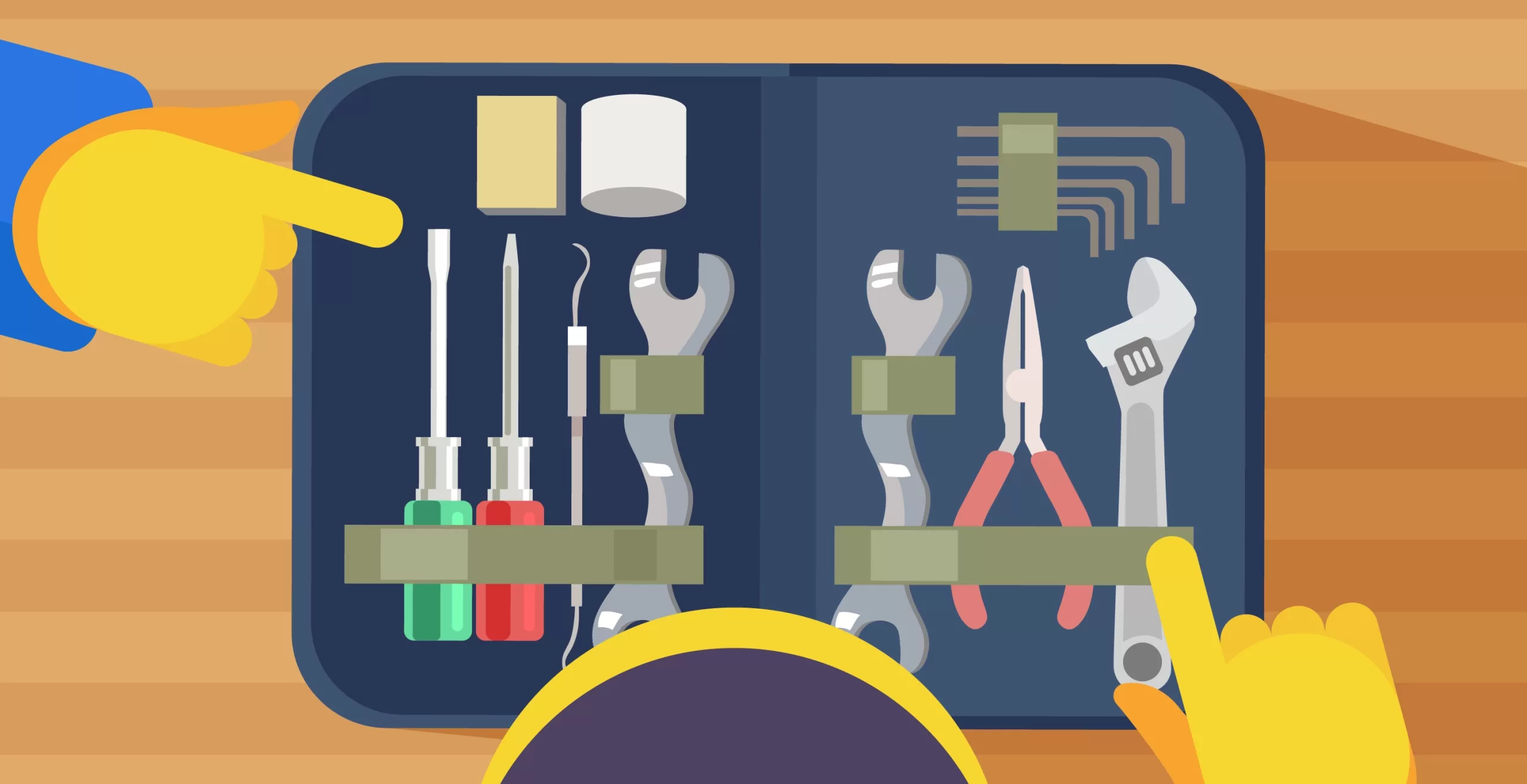
In the vast realm of industrial manufacturing, troubleshooting can seem like a daunting task. However, fear not! We’re here to guide you through the ins and outs of industrial troubleshooting in the simplest way possible.
“Troubleshooting is like solving a puzzle – find the piece, fix the problem.”
Understanding Industrial Troubleshooting
When things go awry on the manufacturing floor, industrial troubleshooting comes into play. It’s like solving a puzzle – identifying and fixing problems to keep the production line running smoothly.
Common Issues in Industrial Manufacturing
Let’s break down some everyday hiccups you might encounter in the industrial landscape:
1. Machinery Jams
Picture this: gears refusing to turn, and belts getting stuck. A machinery jam is like a traffic jam for your equipment. To tackle this, check for debris, lubricate moving parts, and ensure proper alignment.
2. Electrical Glitches
Lights flickering or machines suddenly halting? Electrical glitches can be baffling. Begin by inspecting power connections, looking for loose wires, and testing components. Remember, safety first – always disconnect power before inspecting electrical issues.
3. Fluid Leaks
Fluid leaks can be a messy ordeal. Whether it’s oil, coolant, or hydraulic fluid, identify the source and fix it promptly. Tighten loose connections, replace damaged hoses, and keep the workplace clean to prevent slips.
4. Unusual Sounds
Mysterious clanks and clatters can be concerning. Investigate unusual sounds by listening closely. It might be a loose bolt, worn-out bearing, or a misaligned component. Addressing these early can prevent major breakdowns.
Simple Steps for Effective Troubleshooting
Now that we’ve identified some common issues, let’s delve into uncomplicated steps for effective industrial troubleshooting.
1. Observation is Key
Start by observing the entire system. Look for anything out of the ordinary – odd sounds, unusual smells, or visual abnormalities. A keen eye can often pinpoint the problem area.
2. Follow a Systematic Approach
Don’t dive in blindly! Develop a systematic approach. Begin with the most apparent issues, ruling out possibilities one by one. This methodical process simplifies the troubleshooting journey.
3. Utilize Available Resources
You’re not alone in this. Consult equipment manuals, seek guidance from experienced colleagues, and use online resources. Sometimes, a fresh perspective can provide a simple solution.
4. Keep It Clean
Regular maintenance is your troubleshooting ally. A clean, well-maintained machine is less likely to encounter issues. Schedule routine check-ups and address minor concerns before they escalate.
The Role of Technology in Simplifying Troubleshooting
In our modern era, technology plays a pivotal role in industrial troubleshooting. Let’s explore how it simplifies the process.
1. Predictive Maintenance Systems
Imagine a system that predicts when a machine is about to fail. Predictive maintenance systems utilize sensors and data analysis to foresee potential issues, allowing proactive measures to be taken. It’s like having a crystal ball for your machinery!
2. Remote Monitoring
Technology enables remote monitoring of industrial equipment. This means troubleshooting can happen without physically being present. It’s like having eyes on your machinery 24/7, ensuring issues are tackled swiftly.
3. Augmented Reality (AR) Assistance
AR takes troubleshooting to a whole new level. Technicians can wear AR glasses that provide real-time information and guidance. It’s like having a virtual assistant by your side, simplifying complex tasks.
Ensuring Safety in Troubleshooting
Safety is paramount in industrial troubleshooting. Let’s outline some straightforward safety measures to adhere to.
1. Always Disconnect Power
Before touching anything electrical, disconnect the power source. This simple step prevents accidents and ensures your safety.
2. Wear Personal Protective Equipment (PPE)
Equip yourself with the right gear – safety glasses, gloves, and other PPE. This shields you from potential hazards and keeps you secure during troubleshooting.
3. Follow Standard Operating Procedures (SOPs)
Every industrial setting has SOPs. Stick to them! These procedures are designed to maintain a safe working environment and guide you through troubleshooting processes.
Practical Application
Imagine a factory where machines suddenly stop working. The workers, using the simple troubleshooting steps from our article, identify a loose bolt causing the issue. They tighten it, and voila, the machines are back on track. This practical application showcases how basic troubleshooting can swiftly resolve real-world problems on the factory floor.
Real-world Impact
In a real-world scenario, a manufacturing plant implementing predictive maintenance technology prevents a major breakdown. The system predicts a potential issue, and the technician, guided by the technology, fixes it before it disrupts production. This real-world impact demonstrates how technology simplifies troubleshooting, saving time and resources.
“Technology turns issues into opportunities; predict and prevent breakdowns for seamless production.”
Conclusion: Troubleshooting Made Easy
In the realm of industrial manufacturing, troubleshooting is an inevitable part of the journey. By following simple steps, embracing technology, and prioritizing safety, you can navigate the troubleshooting landscape with confidence. Remember, every issue is a puzzle waiting to be solved – and you’ve got the tools to crack it!

Allen‑Bradley PLC Systems

AC Drive: Variable Frequency Drive

Electrical
