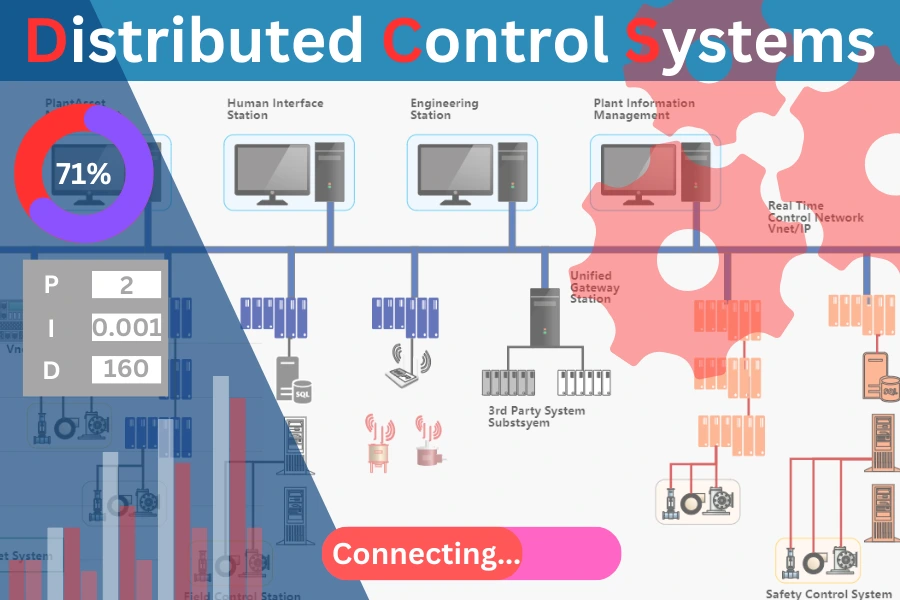
Hey Technicals ! Today, we’re diving into the an interesting world of Industrial Automation as calls: Distributed Control Systems (DCS) from the standpoint of industrial manufacturing. Let’s break down this complex term into bite-sized of easy term to grasp pieces and the parts of technology of automation, lets jump in the sea of DCS and get more about it.
“In the world of manufacturing, DCS is the silent hero, preventing disruptions and keeping the production rhythm in perfect harmony.”
What’s About DCS?
It might sound like some secret code, but it’s really just a super-smart way to control and manage processes in industries like manufacturing. Imagine it as the wizard behind the curtain, making everything run smoothly without you even realizing it.
Decoding DCS: A Simple Overview
At its core, a Distributed Control System is like the conductor of an orchestra. It coordinates various instruments (equipment and machines in our case) to produce a harmonious symphony (a flawless production process). Instead of a single maestro, though, DCS has multiple ‘brain’ centers scattered across the industrial landscape.
The Brainy Setup of DCS
1. Centralized vs. Distributed Control
In the old days, control systems were like a bossy boss, shouting orders from a single central location. On the other hand, spreads the brainpower around, letting different parts of the factory think for themselves – kind of like teamwork, but with machines.
2. Smart Brains Everywhere
Each section of a manufacturing plant has its mini-brain, called a controller. Picture these controllers as tiny geniuses overseeing their specific areas, making quick decisions to keep everything running like a well-oiled machine.
3. Communication is Key
To keep the genius controllers in the loop, they chat with each other. Imagine them passing notes like students in a classroom. This constant communication ensures everyone’s on the same page, preventing chaos and ensuring a smooth operation.
Why Do We Need DCS?
1. Flexibility is King
This is the superhero of adaptability. It allows factories to change the way they operate without major headaches. If the manufacturing game plan needs a tweak, DCS effortlessly adapts, making adjustments without breaking a sweat.
2. Safety First
Safety is non-negotiable in any industry. DCS acts like a vigilant guardian, keeping a watchful eye on equipment conditions. If anything seems off – a machine overheats or a valve misbehaves – DCS jumps in, sounding the alarm before things go haywire.
3. Smooth Sailing Through Failures
Even superheroes stumble sometimes. If one part of the Distributed Control Systems encounters a glitch, the others pick up the slack. It’s like having a team of superheroes – when one rests, the others cover for them, ensuring the show goes on without a hitch.
The Nuts and Bolts: How DCS Works
1. Sensors: The Watchful Eyes
Every hero needs a sidekick, right? Well, Distributed Control Systems has sensors – its trusty sidekicks. These sensors keep tabs on everything, from temperature to pressure, providing real-time updates to the controllers. No sneaky issues go unnoticed!
2. Controllers: The Decision-Makers
Think of controllers as the Sherlock Holmes of DCS. They receive information from the sensors and use their brilliant minds to figure out the best course of action. If something’s amiss, controllers take the reins and set things right.
3. Actuators: The Muscle Power
Now, what good is a plan if it’s not executed? Enter actuators, the strong arms of DCS. When controllers make a decision, actuators spring into action, adjusting valves, turning switches, and ensuring the manufacturing magic happens.
Real-Life DCS Magic: A Story
Let’s imagine a scenario to see DCS in action. Picture a chocolate factory – everyone’s dream, right?
The Chocolate Factory Tale
As the machines churn out delicious chocolate bars, DCS is on high alert. Sensors monitor the temperature of the melting chocolate, controllers analyze the data, and actuators adjust the machinery to maintain the perfect melt.
Suddenly, a sensor detects an anomaly – the cocoa mixer is getting too hot. No need to panic! The controller swiftly sends instructions to the actuator, adjusting the mixer’s speed to cool things down. Crisis averted, and our chocolate bars remain as heavenly as ever.
Advantages of DCS in Industrial Manufacturing
1. Efficiency Boost
DCS is like a productivity coach, optimizing processes for maximum efficiency. With its decentralized intelligence, it fine-tunes operations, ensuring each machine performs at its best.
2. Cost-Effective Brilliance
Efficiency doesn’t just make things smoother; it also saves money. It helps industries cut costs by minimizing energy consumption, reducing waste, and preventing costly downtimes through proactive maintenance.
3. Adaptability for the Win
In the fast-paced world of manufacturing, change is the only constant. Distributed Control Systems thrives on adaptability, allowing industries to evolve without major disruptions. It’s like having a secret weapon for staying ahead of the curve.
The Future of DCS: What to Expect
As technology continues to leap forward, so does DCS. The future promises even smarter, more intuitive systems. Picture DCS evolving into a genius-level strategist, predicting issues before they arise and making split-second decisions for optimal performance.
Practical Application:
Let’s imagine you run a small cookie factory. Without DCS, it’s like baking without a recipe – chaos! With DCS, it’s your trusty baking assistant. Sensors keep an eye on oven temperatures, controllers make sure each batch is perfect, and actuators adjust settings in a snap. It turns your cookie-making process into a well-orchestrated dance, ensuring every cookie comes out just right. Efficiency and deliciousness – that’s the practical magic of DCS!
Real-world Impact:
Consider a car manufacturing plant. Distributed Control Systems plays a vital role in maintaining a smooth operation. Sensors constantly check the assembly line, controllers make split-second decisions, and actuators ensure every part fits seamlessly. Now, imagine a glitch in this system – cars with faulty parts, delays, and unhappy customers. it prevents this nightmare, ensuring cars roll out flawlessly, leaving a positive impact on production, customer satisfaction, and the company’s bottom line.
“Distributed Control Systems turn complexity into simplicity, ensuring each part of the industrial orchestra plays its tune flawlessly.”
Wrapping Up: DCS Unveiled
In the grand theater of industrial manufacturing, Distributed Control Systems takes center stage. From its decentralized intelligence to real-time problem-solving, It is the unsung hero making our everyday products seamlessly. It’s not just about machines; it’s about orchestrating a symphony of efficiency and innovation.
So, the next time you enjoy a chocolate bar, raise a metaphorical toast to DCS, the silent conductor ensuring our world runs smoothly, one production line at a time! Cheers to the unsung heroes of industrial manufacturing!

Sensors
